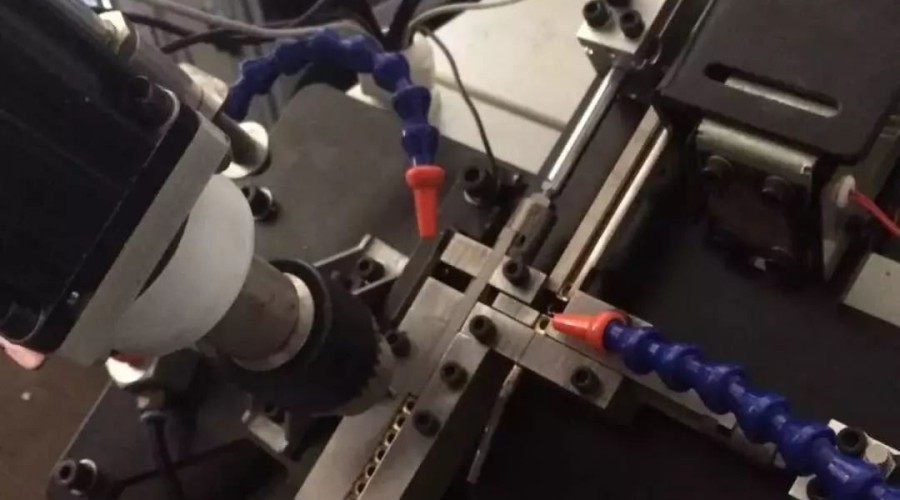
Machine Principle and Description
The automatic tapping machine achieves fully automatic feeding through a vibrating tray or feeder, with pneumatic automatic feed and PLC control of tapping speed and depth. It completes automatic feeding, tapping, and unloading. By adjusting the pneumatic feed speed and time, it achieves speed adjustment for tapping, realizing true unmanned production, saving labor, enabling multi-head collaboration, significantly improving work efficiency, and reducing labor costs.
Features and Scope of Use
This machine has a reasonable structure, and multiple heads work simultaneously, greatly increasing production speed. For threading holes in electrical connectors, a single head can achieve a threading operation of up to 3000 holes per hour. It is easy to operate, safe, reliable, and energy-efficient, suitable for tapping nuts, electronic connectors, fasteners, and other components.
Tapping Machine Principle
Pneumatic tapping machines use compressed air for driving, ensuring safety, speed, and efficiency. They operate at relatively low air pressure and consumption (0.3-0.8 MPa), yet provide high torque output. They can tap threads in various materials such as steel, iron, copper, aluminum, and plastic. Equipped with overload protection, the tapping tool suffers minimal damage, and thread accuracy is high. The machines are easy and convenient to operate, requiring no experience or strength. The machining cost is much lower compared to using CNC machining centers, milling machines with tapping attachments, or manual tapping. Heavy workpieces do not require positioning devices or movement, and the working area is large (radius within 100-2000 mm). They offer rapid positioning, high cutting speed, and increased production volume. Whether it's through holes or blind holes, the tapping process is smooth, and threading can be done vertically or at angles (universal). The machining range is extensive, from M3 to M24. Product longevity is guaranteed.
Maintenance of Tapping Machines
- Regularly drain the air compressor. Regular draining of the air compressor is necessary to prevent excess water from entering the pneumatic motor, which can affect its flexibility over time.
- Ensure regular drainage of the water filter cup of the pneumatic tapping machine.
- Lubricate the oil cup of the dual union piece (the cup on the right). The pneumatic motor of the tapping machine consists of bearings and gears that require lubrication. Proper lubrication ensures smooth operation and durability of the pneumatic tapping machine.
Leave a comment